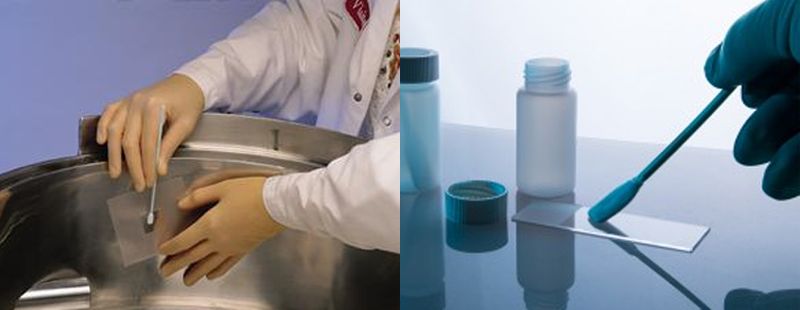
Cleaning validation is carried out not to improve the quality of products but to identify deviations in critical processes and take appropriate corrective actions to ensure the required degree of assurance of product quality. In other words, cleaning validation results point to the need for improvement in manufacturing processes.
Cleaning validation of equipment is performed for new processes, at periodic intervals, when changes have been made based on change control results and quality reviews, taking into consideration risk assessment.
Cleaning validation is documented evidence that an approved cleaning procedure will provide clean equipment suitable for the safe manufacturing of medicinal products.
Validation Center:
-
Conducts an assessment of risks in cleaning validation, prepares justification for the worst-case product selection in the group (products that have a similar route of administration, mechanism of action, pharmacological class, etc.);
-
Performs calculations of MAC and NOAEL as well as acceptance criteria based on the limit of quantification of the most precise analytical method, etc.;
-
Defines the relation between cleaning validation criteria for equipment and metrological characteristics of analytical methods;
-
Determines the approach to cleaning validation; develops cleaning validation master plans (CVMP);
-
Develops the scheme of cleaning validation for equipment, provides statistical data analysis, and validation reports.
-
Carries out GMP audits.
Cleaning validation, key points:
The cleaning validation report contains the calculation of maximum allowable residues of active substances and cleaning detergents, which may be present on the cleaned equipment but do not significantly affect the quality of the subsequent batch or new product produced on this equipment. The sampling program and method to define the recovery efficiency of the sampling method are developed. The concentration of the contaminant defined by the analytical method is calculated, taking into account the area and material of the surface of equipment, which comes in direct contact with the product.
Cleaning validation of equipment verifies the effectiveness of the cleaning procedure to prevent contamination of the subsequent product by the previous product, cleaning agents, or microbial contaminants, and the reproducibility of the selected cleaning procedure.