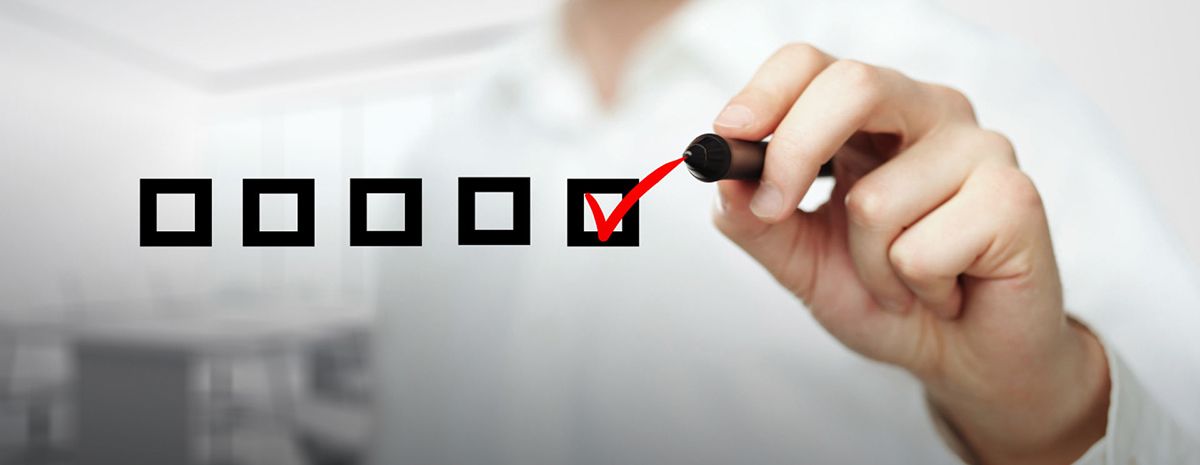
Process validation is performed not to improve the quality of products but to identify non-conformities at the critical stages of the process and take appropriate corrective actions to ensure the required degree of assurance of product quality. In other words, process validation results point to the need for improvement in manufacturing processes.
Process Validation is defined as documented evidence that the process, operated within established parameters, can perform effectively and reproducibly to produce a medicinal product meeting its predetermined specifications and quality attributes.
Process validation is performed for new processes and when changes have been made based on change control results and quality reviews, taking into account risk assessment.
Process validation:
-
Process validation (manufacturing process validation) of medicinal products, biopharmaceuticals, dietary supplements, medical devices, etc.;
-
Process validation for cleanroom garments, definition of optimal cycle parameters: inspection/washing/drying/stocking/sterilization/supply;
-
Process validation for the transfer of samples to cleanrooms, determination of decontamination time of pass boxes.
Key points
Process validation can be prospective (renovated manufacturing facility, before launch) and concurrent (routine manufacturing process).
According to the latest version of GMP regulations, retrospective validation is no longer considered an acceptable approach.
Process validation of pharmaceuticals is the concept closely connected and based on GMP rules and is the final stage of validation performed after completing all qualification stages.
While performing process validation, specialists of Validation Center preliminary carry out a thorough analysis to identify critical processes, the failure of which can affect the quality of manufactured products and critical parameters of one specific process, change of which may cause a deviation in product quality.
For instance, critical processes for the manufacture of film-coated tablets are preparation of granulated material, tabletization, and coating. The critical parameters having an impact on the quality of these processes are granulation parameters (temperature, time, granulation liquid feed rate, etc.), press operating parameters (pressing force and capacity), and critical parameters of coating (film-forming material feed rate, number of revolutions, load factor, temperature, etc.).
The results of process validation should be presented in the report in which the evaluation of the correctness of established process parameters, evaluation of accuracy and adequacy of process methods, evaluation of equipment capacity to ensure that it is capable of meeting the process parameters, evaluation of process parameters reproducibility thereby ensuring the required quality attributes are summarized.
Validation of management systems
Validation of management systems (process to ensure the correctness of specifications, design and product) is defined as activities that are gaining ever-increasing importance. Validation is a key tool to support quality control of the entire system.