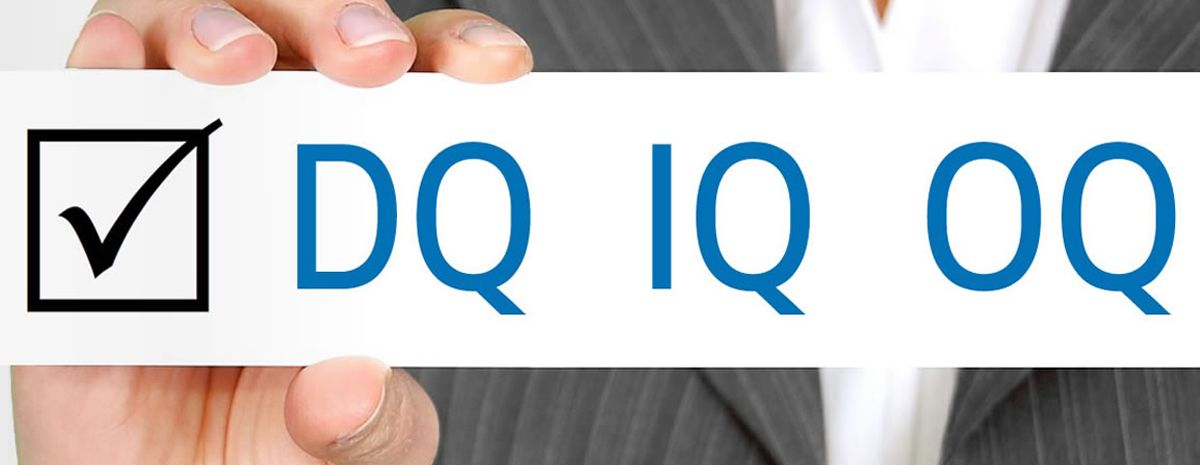
Qualification is documented evidence that a specific equipment and/or system operates correctly, gives reproducibility, and leads to the expected results.
Qualification tends to be smaller in scope than validation and defines a separate direction related to the testing of the parameters of utilities, manufacturing premises, process and laboratory equipment, and other facilities to ensure their compliance with GMP standards and other regulations governing safe production of medicinal products of the desired quality.
Qualification of premises, utilities, equipment and laboratories:
Cleanrooms and clean zones |
|
Utilities |
|
Sterilization equipment |
|
Pharmaceutical manufacturing equipment |
|
R&D/QA laboratories |
|
Main stages of qualification:
-
Design qualification (DQ) is a documented verification that the proposed design of the facilities, systems and equipment (utilities, warehouse, etc.) meets the requirements of the User Requirements Specification (URS) and GMP.
-
Installation Qualification (IQ) is a documented verification that the facilities, systems, or equipment as installed or modified, comply with the approved design and other technical documentation.
-
Operational Qualification (OQ) is a documented verification that the facilities, systems, or equipment, as installed or modified, perform as intended throughout the anticipated operating ranges.
-
Performance Qualification (PQ) is a documented verification that the facilities, systems, or equipment, as connected together, can perform effectively and reproducibly based on the approved process method, master production instructions, and product specifications.
We also arrange visits to perform FAT (Factory Acceptance Test) at the manufacturer's site and SAT (Site Acceptance Test) at the customer's site.
The most in-demand qualifications in the pharmaceutical industry are:
-
Qualification of syrup filling lines;
-
Qualification of aerosol and spray productions;
-
Qualification of packaging equipment;
-
Qualification of blister packing machines;
-
Qualification of carton packing machines;
-
Qualification of thermostats;
-
Qualification of incubators;
-
Qualification of environmental chambers;
-
Qualification of laboratory sterilizers.
Qualification documentation:
Qualification protocol is a document describing qualification activities to be performed for testing as well as defining specific parameters to be assessed, acceptance criteria of each of these parameters, assessment criteria, methods of measurement and measuring instruments, including information about their precision, verification and calibration.
Qualification report is a document in which the results of completed qualification activities, initial information about the qualification object, analysis of obtained data, proposals for conducting requalification and conclusions are assembled.