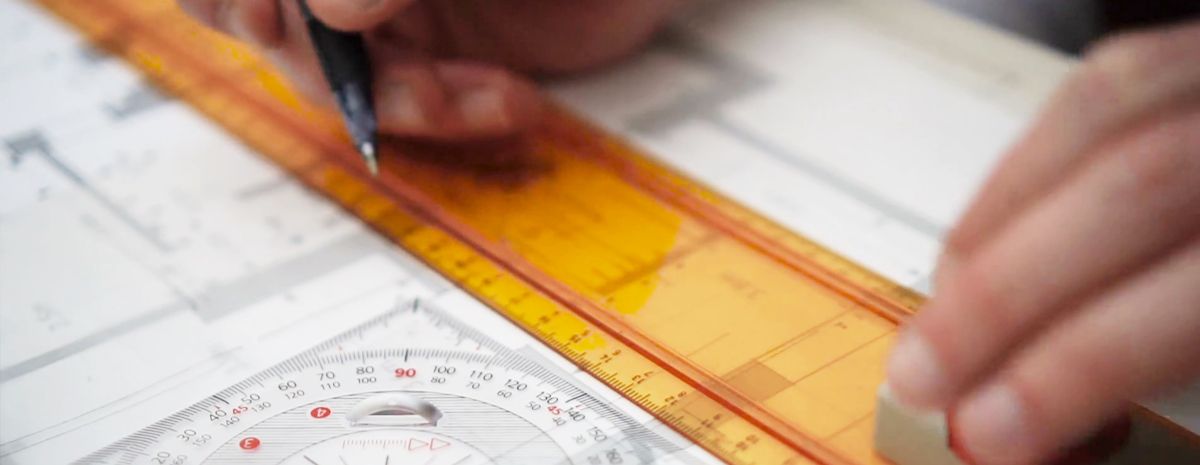
“The first element of the validation of new facilities, systems, or equipment could be design qualification (DQ). The compliance of the design with GMP should be demonstrated and documented.”
EU GMP, Annex 15: Qualification and validation
Design qualification (DQ) is a documented verification that the proposed design of the manufacturing facilities (utilities, equipment, warehouse, etc.) meets the User Requirements Specification (URS) and GMP.
The key aspects of design qualification involve:
-
Verification of the process continuity;
-
Minimization of the risk of contamination;
-
Organization of materials & personnel flow;
-
Ensuring the correctness of the classification of cleanroom grades;
-
Pressure differential between rooms;
-
Provision of the opportunity for effective cleaning of equipment and facilities;
-
Maximum grouping of facilities of the same cleanliness classification;
-
Efficient placement of equipment and materials to prevent mix-ups between different components, batches of raw materials, packaging materials, etc.
We perform design qualification of the following objects:
-
Manufacture of pharmaceuticals;
-
Manufacture of veterinary products;
-
Quality control laboratories;
-
Warehouses;
-
Utilities (water, air, steam);
-
Ventilation and air conditioning systems for cleanrooms.
Why perform?
According to the latest version of GMP, the User Requirements Specification (URS) should be a point of reference throughout the validation life cycle. At this stage, it is necessary to lay down the basic elements of quality and to reduce any GMP risks to an acceptable level. Besides, the User Requirements Specification should be checked for compliance with GMP standards.
Design qualification is the mandatory stage of qualification! In most cases, it is reasonable first to conduct conceptual design qualification and then working design qualification. In addition, design qualification must be completed before commencing the construction of the designed project.
In terms of economic risks, imagine a situation when the design does not cover all GMP requirements or, in the worst case, contains incorrect and inapplicable to industry solutions. After implementing this design, the expenses spent on reconstruction will be a hundred, a thousand times more than the cost of the design qualification. Are you ready to go to all that expense?
The most in-demand design qualifications:
-
Design qualification for cleanrooms;
-
Design qualification for manufacturing objects;
-
Design qualification for ventilation systems;
-
Design qualification for laboratories;
-
Design qualification for microbiology laboratories.
Who can and who should perform?
Please note that validation activities are not licensed (any company can provide these services). You may conduct the validation by yourself or order this service from a company that performs validation activities. The other question is competence, a sufficient number of trained personnel, work experience, and objectivity in assessment. These factors need to be considered when choosing a DQ subcontractor.