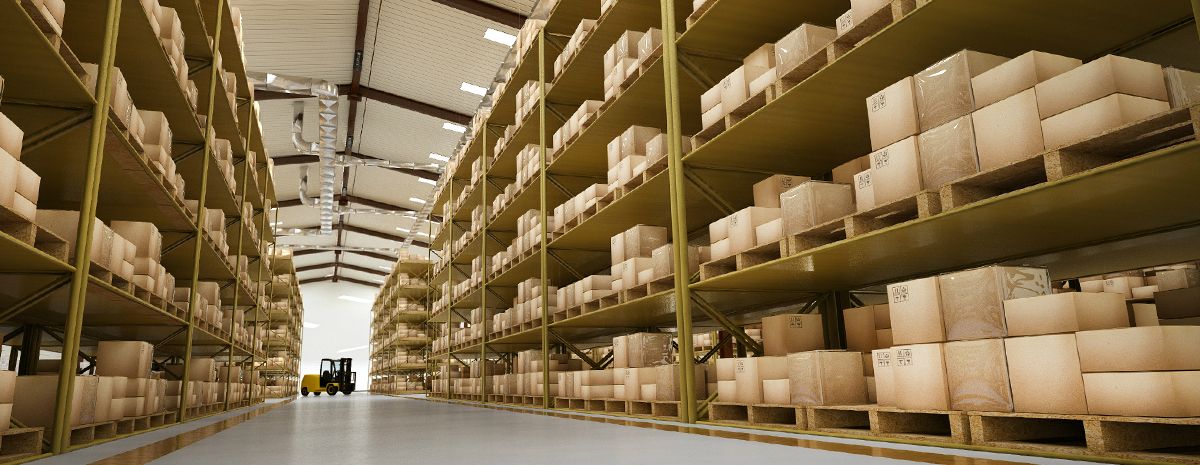
According to many international regulations (GMP, GDP, and GSP), qualification of storage areas (pharmaceutical warehouse, pharmacy depot, and distributor's warehouse) must be conducted. The purpose of warehouse qualification is to ensure that storage conditions for pharmaceutical products and materials comply with the labeling and consider air temperature and relative humidity requirements.
Warehouse qualification is documented evidence that storage conditions for products are maintained across the entire warehouse space, on each rack, and in the places where the products are stored.
The heating, ventilation, and air conditioning system in a pharmaceutical warehouse must maintain the set temperature and, if necessary, air humidity, regardless of the time of day, day of the week, or the climatic season. Therefore, warehouse qualification should embrace these conditions and should be carried out at least for the two most critical climatic seasons, when the ambient temperature is higher or lower than the product storage temperature in a warehouse, which corresponds to the operation of cooling systems in the warm period of the year and heating systems in the cold period of the year. Transport qualification may be performed, if necessary.
Warehouse qualification
Design qualification can be the first stage of warehouse qualification. It is carried out before the start of construction and involves the analysis of design documentation. This stage is not mandatory, but critical errors, which will not be easy to correct after design implementation, if possible at all, can be identified during this stage.
Installation qualification is performed for new warehouses or warehouses after renovation. Visual inspection and comparison against specifications are mainly used during this stage. The availability of design documentation, operating and maintenance manuals for ventilation systems, air coolers, heaters, automation and dispatch systems is checked. Besides, verification of the installation of rooms, equipment, piping, and auxiliary systems against the engineering drawings and specifications is carried out.
According to GDP, it is necessary to define calibration requirements for monitoring instruments and temperature monitoring systems and check if calibration certificates are available during this qualification phase. We recommend to separate the processes of warehouse qualification and monitoring system installation since the latter should be carried out after warehouse qualification and identification of critical control points. Do not forget that a monitoring system also requires qualification, which is a completely different process.
Operational qualification begins after successful completion of installation qualification. Mapping of storage areas using wireless temperature and humidity data loggers is performed at this stage. It is not correct to use thermal cameras for this process; infrared thermometers can only be considered an additional risk analysis tool. By its nature, warehouse mapping is the identification of the coldest and hottest spots as well as the spots where the maximum temperature fluctuations occur. These measurements are carried out for at least 24 hours with a measurement interval of 5-15 minutes. The number of data loggers is determined individually for each storage area.
Critical control points where monitoring system sensors should be located must be determined for the warehouse in an empty state based on mapping results.
Following the successful completion of OQ, written procedures (SWP, SOP) should be in place; all operations that are not related to distributor activities should be completed, and operator training should be performed. All these factors will allow using a pharmaceutical warehouse.
Performance qualification is conducted after the successful completion of installation and operational qualification. Mapping of the storage area in a similar way as for OQ only for the warehouse in its loaded state is performed. Measurements are carried out for at least 72 hours. The warehouse should be loaded as maximum as possible to define the worst-case scenario in terms of air circulation obstruction, which is usually more than 60%.
Based on qualification results, critical control points to install additional monitoring system sensors must be determined for the warehouse in a loaded condition, if they differ from those defined during operational qualification.
Performance qualification should be conducted at least in the warm and cold periods of the year to verify heating and cooling system operation. If the heating, ventilation, and air conditioning system is equipped with an automatic switchover between heating and cooling modes, it is necessary to perform qualification three times a year:
-
During a cold period - in winter, when the average daily ambient temperature is below the storage temperature;
-
During a warm period - in summer, when the average daily ambient temperature is higher than the storage temperature;
-
During a transition period: autumn/winter or winter/spring, when the temperature at night drops below the storage temperature, and during the daytime - above the storage temperature.
Warehouse requalification
The frequency of qualification has to be established based on risk assessment, change control, and monitoring system data reviews according to GDP standards. In practice, however, risk assessment is conducted as a formality where the outcome is known beforehand and intended to ensure that “nothing has changed” and change control system functions, at its best, under the cumulative system. Change management is not the case here, and monitoring system data reviews are carried out without performing trend analysis and only under the principle "within the specified limits". As a result, in most cases, the frequency of qualification once every two, three, or more years is not justified; and many deviations can be found during the qualification of such warehouses.
The best way to optimize the planning and arrange qualification of a distributor of medicinal products is to establish the frequency of requalification, which would cover warm and cold periods throughout every year, to obtain sufficient statistics that allow to reduce the frequency of requalification.
Monitoring system
A monitoring system is a system whose product is the current information on technical state of equipment and its hazards given with essential comments (prediction of remaining useful life, emergency procedures for personnel, etc.) and established risks.