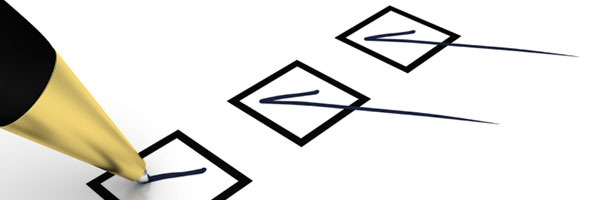
The main business activities of our company are validation and qualification. We have the necessary qualifications, experience, and an instrumental base. Validation Center has successfully completed more than 1000 projects. We perform validation and qualification regularly and are sure of the results we obtain.
Validation and qualification are the actions of proving, in accordance with the principles of GMP, that a specific procedure, process, equipment, material, activity, or system actually leads to the expected results.
We specialize in:
-
Design Qualification;
-
Qualification of cleanroom and clean zones, utilities, pharmaceutical and medical equipment, quality control lab equipment, microbiology lab equipment;
-
Validation and qualification of pharmaceutical warehouses, cold rooms, freezers, refrigerated road vehicles, insulated shipping containers;
-
Process validation, cleaning validation, validation of aseptic processing, validation of sterilization processes;
-
Cold chain validation;
-
Validation of computerized systems (IT-validation).
Validation and qualification, main stages:
-
Design qualification (DQ) is a documented verification that the proposed design of the facilities, system, equipment, warehouse, etc. meets the requirements of the User Requirements Specification (URS) and GMP.
-
Installation Qualification (IQ) is a documented verification that the facilities, systems, and equipment as installed or modified, comply with the approved design and other technical documentation.
-
Operational Qualification (OQ) is a documented verification that the facilities, systems, and equipment, as installed or modified, perform as intended throughout the anticipated operating ranges.
-
Performance Qualification (PQ) is a documented verification that the facilities, systems, and equipment, as connected together, can perform effectively and reproducibly based on the approved process method, master production instructions, and product specifications.
-
Process Validation, PV is defined as documented evidence that the process, operated within established parameters, can perform effectively and reproducibly to produce a medicinal product meeting its predetermined specifications and quality attributes.
-
We also arrange visits to perform FAT (Factory Acceptance Test) at the manufacturer's facility and SAT (Site Acceptance Test) at the customer's facility.
Validation, qualification and work planning
According to GMP regulations, it should be identified what validation work is needed to prove that critical aspects of particular operations are appropriately controlled. Significant changes to the facilities, equipment, and processes that may affect the quality of the product should be validated. A risk assessment approach should be used to determine the scope and extent of validation required.
All validation and qualification activities should be planned. The key elements of the validation and qualification program must be clearly defined and documented in the Validation Master Plan (VMP).
We have the necessary resources to perform validation and qualification successfully:
-
Our validation and qualification laboratory is equipped with modern high-precision measuring equipment, which is regularly calibrated.
-
All measurements and processing of results are carried out using specialized software, thus preventing errors committed by operators and significantly reducing the time to perform qualification.
-
The specialists of our company are professionals in the sphere of validation and qualification, GMP, GDP, pharmaceutical technologies, design, construction, commissioning, operation of cleanrooms and zones, cleanroom utility systems, and process equipment.