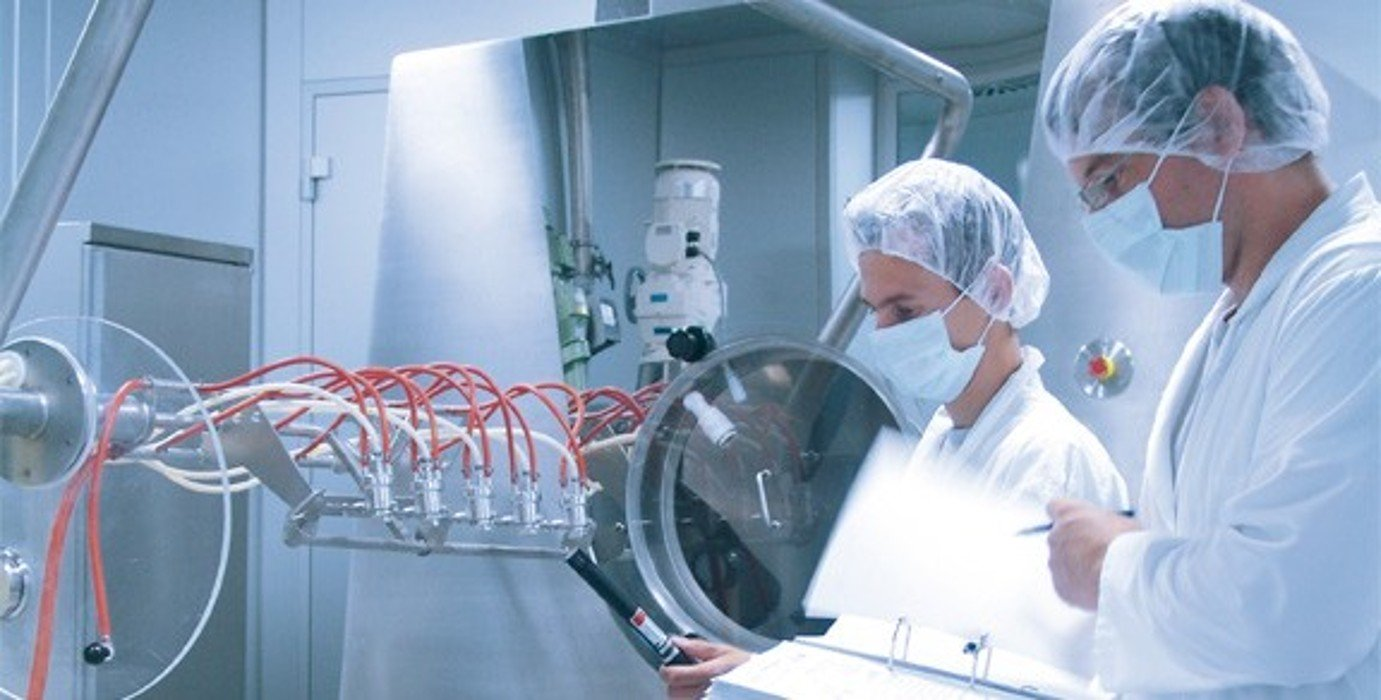
Фармацевтическая промышленность давно столкнулась с необходимостью проведения валидации критических объектов (валидация фарм производства), т.е. объектов, которые оказывают прямое или косвенное влияние на качество производимой продукции или на результаты проверки качества этой продукции.
К таким объектам относится практически все производственное и лабораторное оборудование, системы получения чистых сред (чистый пар, чистый сжатый воздух, азот, вода очищенная, вода для инъекций и др.), чистые помещения и обеспечивающая их система вентиляции, кондиционирования и отопления, а также компьютеризированные системы. К этому перечню следует добавить оборудование, используемое в фармацевтическом производстве и разработке, климатические условия складов и архивов образцов продукции. Следует упомянуть также о валидации технологических процессов, процессов очистки и валидации аналитических методик.
Как мы видим, перечень довольно обширный, учитывая, что на предприятии обычно функционирует не один производственный участок и производится не одно наименование лекарственного средства.
Такой колоссальный перечень объектов требует от предприятия серьезной работы в планировании валидации, в процессе которой на первый план выходят срок, к которому следует окончить проведение работ и требуемые для валидации ресурсы.
Не будем останавливаться на обычно очень сжатых сроках, которые индивидуальны для каждого завода или даже участка. Давайте рассмотрим наиболее важные ресурсы. На первом месте, как и в любом деле, стоит персонал, за которым, на наш взгляд, идет валидационное оборудование и расходные материалы.
Валидация фарм производства также затрагивает трудности, связанные с персоналом, занятым валидацией, в основном не отличаются от проблем связанных с любым другим делом. Это поиск, наем на работу, оснащение рабочих мест и, самое важное — обучение. Именно с обучением связаны основные сложности. Подготовленных специалистов по валидации ВУЗы не выпускают. Поэтому необходимо дожидаться семинаров и тренингов, специализированных на вопросах валидации. Довольно длительное самообучение методом проб и ошибок может быть слишком рискованным в плане получения критических и существенных несоответствий при проверке инспектирующими органами.
Валидация фарм производства требует наличия соответствующего оборудования. Ниже представлен минимальный перечень валидационного оборудования, который позволяет проводить квалификацию подавляющего большинства критических объектов: счетчик аэрозольных частиц, генератор аэрозольных частиц, разбавитель (дилутор), баллометр, анемометр, дифференциальный манометр, генератор тумана, видеокамера, регистраторы температуры и влажности, регистраторы для валидации стерилизаторов, калибратор, тахометр и др.
Кроме необходимости приобретения данного оборудования необходимо учитывать расходы, связанные с закупкой расходных материалов, регулярной калибровкой, поверкой измерительных приборов и возможных расходов, связанных с обслуживанием и ремонтом оборудования.
Завершив рассматривать требуемые ресурсы, давайте кратко остановимся на минимально необходимом объеме валидации. Как мы упоминали ранее, валидация фарм производства должна охватывать критические объекты. Но это не дает ответ, в каком объеме следует валидировать тот или иной объект. То есть каким валидационным испытаниям и проверкам следует подвергнуть объект валидации, а каким нет. Конечно, можно не тратить время на рассуждения и подвергнуть испытаниям все подряд. Но тогда будет потрачено излишнее количество ресурсов, наиболее важное из которых, в данном случае, время. За это время можно бы было продвинуться далеко вперед, выполняя график валидации.
Объем валидации должен определяться исходя из выводов анализа рисков. Это значит, что следует проверять (подвергать валидационным испытаниям) только те характеристики и функции объекта, которые оказывают влияние на качество получаемого продукта и, в конечном итоге, на лекарственное средство. Таким образом, во время планирования работ по валидации следует оценить необходимый объем валидации для каждого объекта, который позволит объективно сделать заключение о соответствии или несоответствии валидируемого объекта заранее установленным требованиям. Установленный объем валидации следует отразить в Основном плане валидации.
Неправильным будет не сказать, что для наиболее критических объектов, например, чистые помещения, стерилизаторы и др., приняты международные стандарты, которые регламентируют требования, которым должны отвечать испытуемые объекты, а также методологию оценки соответствия этим требованиям.
Понимая трудности решения проблем валидации, с которыми в последнее время так остро столкнулись фармацевтические производства, необходим поиск оптимизации затрат для получения требуемого результата в ограниченные сроки. Одним из решений данной проблемы является привлечение в качестве подрядчиков сторонних предприятий, специализирующихся на работах по валидации. Это решение не избавляет фарм производителей от необходимости использования собственных сил для работ по валидации, но позволяет в краткие сроки решить остро вставшую необходимость валидации тех или иных объектов. При этом собственные сотрудники могут параллельно получить практические знания и навыки по проведению валидации. Последнее не мало важно в перспективе организации и проведения работ по валидации, а также поспособствует положительному общению с инспекторами в процессе проверки отчетов по валидации.
Что касается работ по валидации, предприятие может пойти по пути аутсорсинга. Таким образом предприятие избавляете себя от проблем отслеживания постоянно меняющихся требований к валидации и перекладывает ответственность за это на подрядную организацию. Другой альтернативой является построение работы дифференцировано. Собственные сотрудники занимаются планированием и проведением валидации технологических процессов и процессов очистки, а к сторонним организациям обращаются только для проведения валидации инструментальными методами (квалификация оборудования). Такой подход позволяет собственным сотрудникам понимать и применять результаты валидации на стадиях разработки, регистрации и перерегистрации препаратов, т.к. собственные специалисты принимают непосредственное участие в работах по валидации.
Возвращаясь к рассматриваемой теме, можно подытожить, что каждое фармацевтическое производство выбирает свой путь оптимизации затрат и времени для решения проблем валидации.