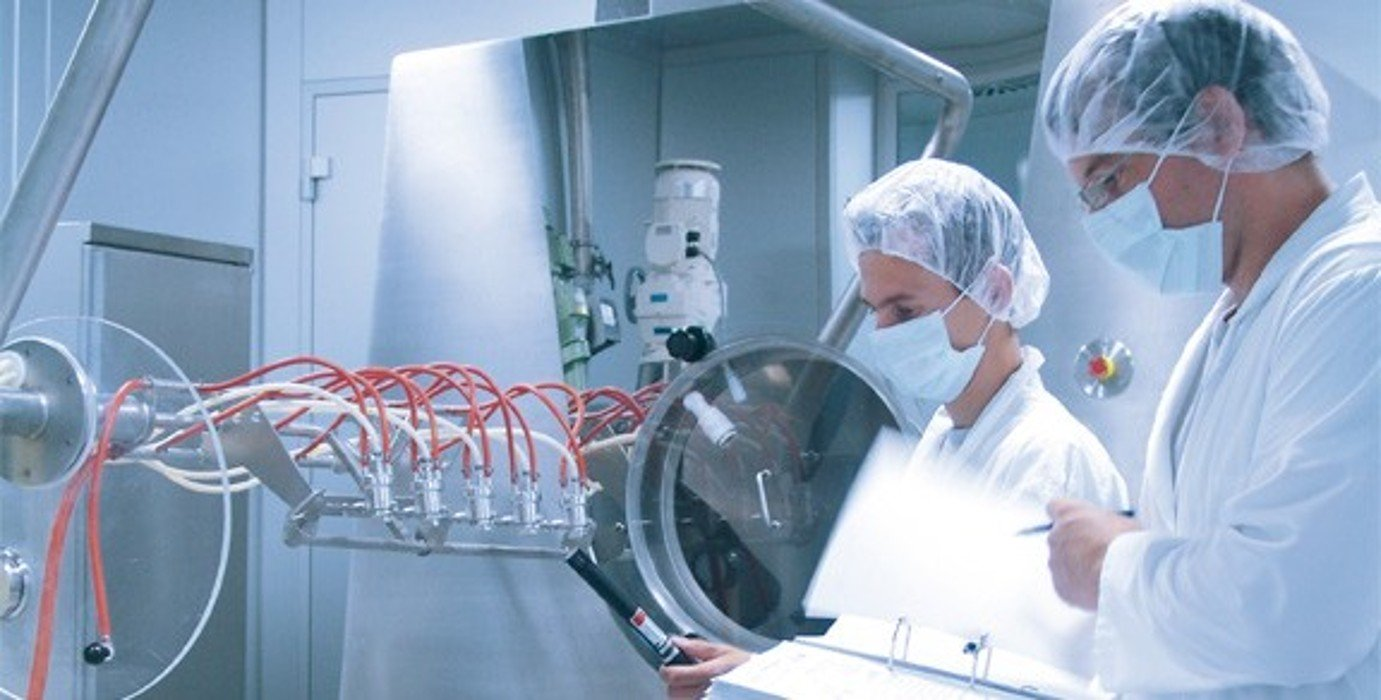
Фармацевтична промисловість давно зіткнулася з необхідністю проведення валідації критичних об'єктів (валідація фарм виробництва), тобто об'єктів, які мають прямий або опосередкований вплив на якість виробленої продукції або на результати перевірки якості цієї продукції.
До таких об'єктів належить практично все виробниче і лабораторне обладнання, системи отримання чистих середовищ (чистий пар, чисте стиснене повітря, азот, вода очищена, вода для ін'єкцій та ін.), чисті приміщення і система вентиляції, що забезпечує їх, кондиціонування та опалення, а також комп'ютеризовані системи. До цього переліку слід додати обладнання, що використовується у фармацевтичному виробництві та розробці, кліматичні умови складів і архівів зразків продукції. Слід згадати також про валідацію технологічних процесів, процесів очищення і валідацію аналітичних методик.
Як ми бачимо, перелік досить великий, враховуючи, що на підприємстві зазвичай функціонує не одна виробнича ділянка і виробляється не одне найменування лікарського засобу.
Такий колосальний перелік об'єктів вимагає від підприємства серйозної роботи в плануванні валідації, в процесі якої на перший план виходять термін, до якого слід завершити проведення робіт і необхідні для валідації ресурси.
Не будемо зупинятися на зазвичай дуже стислих термінах, які індивідуальні для кожного заводу або навіть ділянки. Давайте розглянемо найбільш важливі ресурси. На першому місці, як і в будь-якій справі, стоїть персонал, за яким, на наш погляд, йде валідаційне обладнання та витратні матеріали.
Валідація фарм виробництва також зачіпає проблеми, пов'язані з персоналом, зайнятим валідацією, в основному не відрізняються від проблем, пов'язаних з будь-якою іншою справою. Це пошук, прийняття на роботу, оснащення робочих місць і, найважливіше - навчання. Саме з навчанням пов'язані більшість складностей. Підготовлених фахівців з валідації ВНЗ не випускають. Тому необхідно чекати семінарів і тренінгів, спеціалізованих на питаннях валідації. Досить тривале самонавчання методом проб і помилок може бути занадто ризикованим в плані отримання критичних та суттєвих невідповідностей під час перевірки органами інспекції.
Валідація фарм виробництва вимагає наявності відповідного обладнання. Нижче представлений мінімальний перелік валідаційного обладнання, яке дозволяє проводити кваліфікацію переважної більшості критичних об'єктів: лічильник аерозольних часток, генератор аерозольних часток, розчинник (ділутор), баллометр, анемометр, диференційний манометр, генератор туману, відеокамера, реєстратори температури і вологості, реєстратори для валідації стерилізаторів , калібратор, тахометр та ін.
Крім необхідності придбання даного обладнання необхідно враховувати витрати, пов'язані із закупівлею витратних матеріалів, регулярним калібруванням, повіркою вимірювальних приладів і можливих витрат, пов'язаних з обслуговуванням і ремонтом обладнання.
По завершенню огляду необхідних ресурсів, давайте стисло зупинимося на мінімально необхідному обсязі валідації. Як ми згадували раніше, валідація фарм виробництва повинна охоплювати критичні об'єкти. Але це не дає відповідь, в якому обсязі слід затверджувати той чи інший об'єкт. Тобто яким валідаційним випробуванням і перевіркам слід піддати об'єкт валідації, а яким ні. Звичайно, можна не витрачати час на міркування і піддати випробуванням все підряд. Але тоді буде витрачена зайва кількість ресурсів, найбільш важливий з яких, в даному випадку, час. За цей час можна було б просунутися далеко вперед, виконуючи графік валідації.
Обсяг валідації повинен визначатися виходячи з висновків аналізу ризиків. Це означає, що слід перевіряти (піддавати валідаційним випробуванням) тільки ті характеристики і функції об'єкта, які впливають на якість одержуваного продукту і, наприкінці, на лікарський засіб. Таким чином, під час планування робіт з валідації слід оцінити необхідний обсяг валідації для кожного об'єкта, який дозволить об'єктивно зробити висновок про відповідність або невідповідність об'єкта, що валідується заздалегідь встановленим вимогам. Встановлений обсяг валідації слід відобразити в Основному плані валідації.
Неправильним буде не сказати, що для найбільш критичних об'єктів, наприклад, чисті приміщення, стерилізатори та ін., прийнято міжнародні стандарти, які регламентують вимоги, яким повинні відповідати випробовувані об'єкти, а також методологію оцінки відповідності цим вимогам.
Розуміючи труднощі вирішення проблем валідації, з якими останнім часом так гостро зіткнулися фармацевтичні виробництва, необхідний пошук оптимізації витрат для отримання необхідного результату в обмежені терміни. Одним з варіантів розв'язання даної проблеми є залучення в якості підрядників сторонніх підприємств, що спеціалізуються на роботах по валідації. Це рішення не позбавляє фарм виробників від необхідності використання власних сил для робіт по валідації, але дозволяє у стислі терміни вирішити гостру необхідність валідації тих чи інших об'єктів. При цьому власні співробітники можуть паралельно отримати практичні знання та навички з проведення валідації. Останнє не менш важливо в перспективі організації та проведенні робіт з валідації, а також посприяє позитивному спілкуванню з інспекторами в процесі перевірки звітів з валідації.
Стосовно робіт з валідації, підприємство може піти за шляху аутсорсингу. Таким чином підприємство позбавляєте себе від проблем відстеження постійно мінливих вимог до валідації і перекладає відповідальність за це на підрядну організацію. Іншою альтернативою є побудова роботи диференційовано. Власні співробітники займаються плануванням і проведенням валідації технологічних процесів і процесів очищення, а до сторонніх організацій звертаються тільки для проведення валідації інструментальними методами (кваліфікація обладнання). Такий підхід дозволяє власним співробітникам розуміти і застосовувати результати валідації на стадіях розробки, реєстрації та перереєстрації препаратів, тому що власні фахівці беруть безпосередню участь в роботах по валідації.
Повертаючись до теми, можна підсумувати, що кожне фармацевтичне виробництво вибирає свій шлях оптимізації витрат і часу для вирішення проблем валідації.